PROTECTED AGAINST ABRASION & WEAR
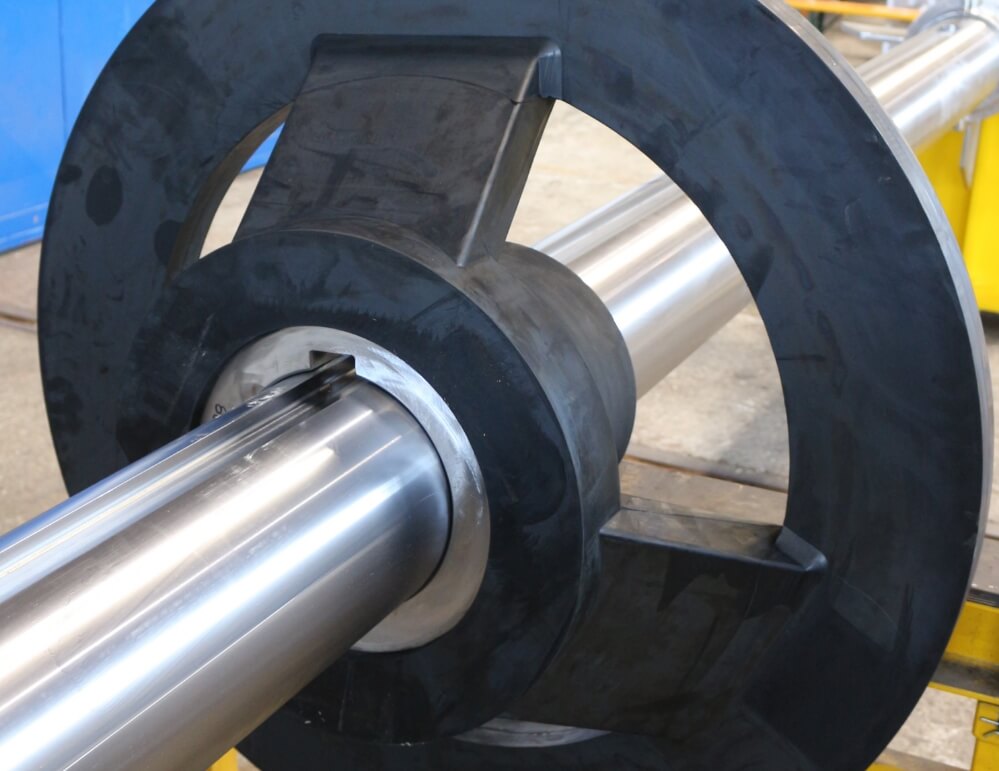
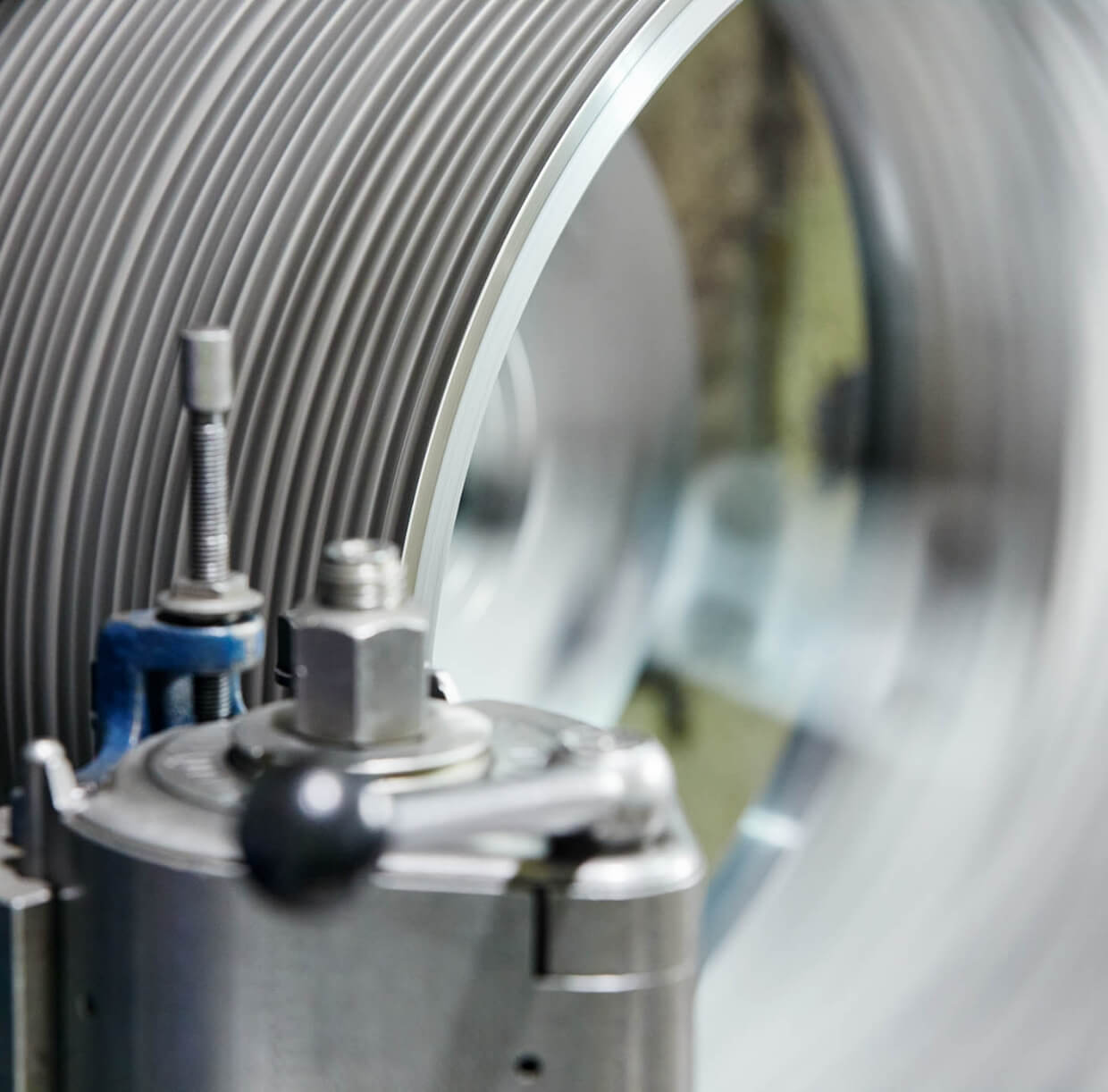
KMF offers leading system solutions for hard and soft wear protection. Our manufacturing methods ensure a reliable and effective wear protection solution for a wide range of applications and industries.
WEAR PROTECTION WITH HARD MATERIALS
DURABILITY &
RESISTANCE
Wear protection with hard materials includes various methods for extending the service life of components and improving their abrasion resistance.
COMMON METHODS
Your title
Your content goes here. Edit or remove this text inline or in the module Content settings. You can also style every aspect of this content in the module Design settings and even apply custom CSS to this text in the module Advanced settings.
WELDING ARMOR
Components can be made more flexible by applying hard material such as chrome-boron welding wire using welding technology. Our protective coating offers high abrasion resistance and can be used on a variety of surfaces.
FLAME SPRAYING
We use a sintering process during flame spraying to apply materials such as tungsten carbide to surfaces. This coating offers a combination of wear and corrosion protection and is ideal for demanding applications.
SOLDERING HARD METAL PLATES
Another way to create a resistant surface is to solder hard metal plates. When soldering, hard metal plates, such as those made of tungsten carbide, are firmly bonded to the base body. This method offers very high hardness and abrasion resistance, especially for components that are subject to heavy use.
APPLYING CERAMIC PLATES
Attaching ceramic plates made of aluminium oxide, silicon nitride or silicon carbide, for example, creates a robust wear protection layer. This method is particularly suitable for applications where high chemical resistance and wear resistance are required.
WEAR PROTECTION WITH SOFT MATERIALS
PROTECTION FOR THE MOST DEMANDING REQUIREMENTS
Wear protection with soft materials includes various methods to protect the surfaces of components from abrasion and wear.
Polyurethane coatings offer high abrasion and wear resistance. These coatings are ideal for industrial applications where high mechanical stress occurs.
The coating is usually applied to a steel base body using a hot-casting process. For optimum adhesion, it is recommended to apply special rubber compounds (rubber) to the steel base body using high-pressure vulcanisation. Rubber coatings are extremely elastic and offer excellent shock absorption and high tear resistance.
Rubber products are often used in areas where flexibility and resistance to mechanical stress are required, such as in the construction and mining industries.
Depending on the specific requirements of the application, special compounds that have certain properties such as chemical resistance, temperature resistance or non-stick properties, can also be used.

Each of these methods has specific advantages and is suitable for different applications and operating conditions. The choice of the appropriate method depends on the specific requirements of the application, such as the type of wear, load and environmental influences.