ALUMINIUM TECHNOLOGIES
NEW POSSIBILITIES IN RECYCLING
The recycling of aluminium significantly reduces CO2 emissions. By recycling 2 million tonnes of secondary aluminium, around 30 million tonnes of CO2 could be saved annually, with 4.5 million tonnes being saved through sufficient slag cooling alone.
When aluminium is melted, a skin of aluminium oxide is formed, which is called “dross”. This contains a lot of recyclable metallic aluminium that should be recovered.
The innovative MASTERmax furnace technology developed by KMF opens up new possibilities in recycling and offers the highest efficiency in the thermal processing of non-ferrous metals (aluminium, zinc, copper, lead), as well as their slag, chips, dross and other residues.
KMF builds special processing systems for hot, salt-free processing of aluminium dross, exclusively for TAHA International Corporation. These systems do not require any additional thermal energy and are therefore extremely cost-effective.

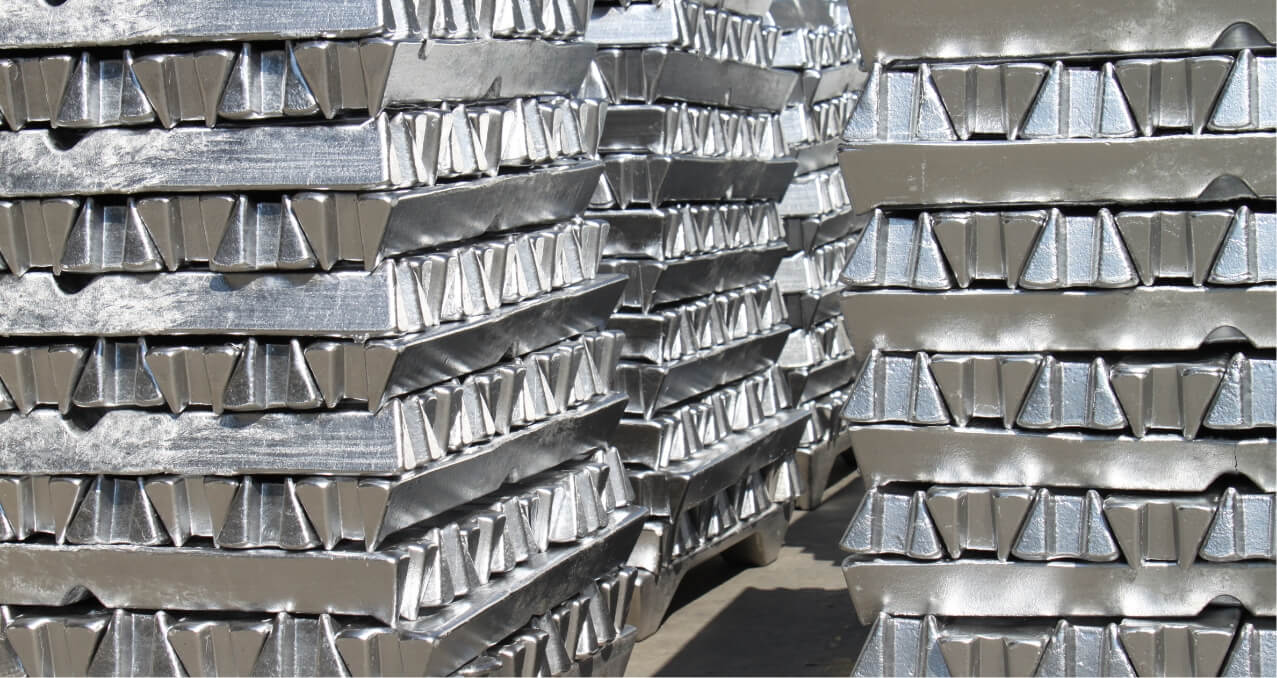
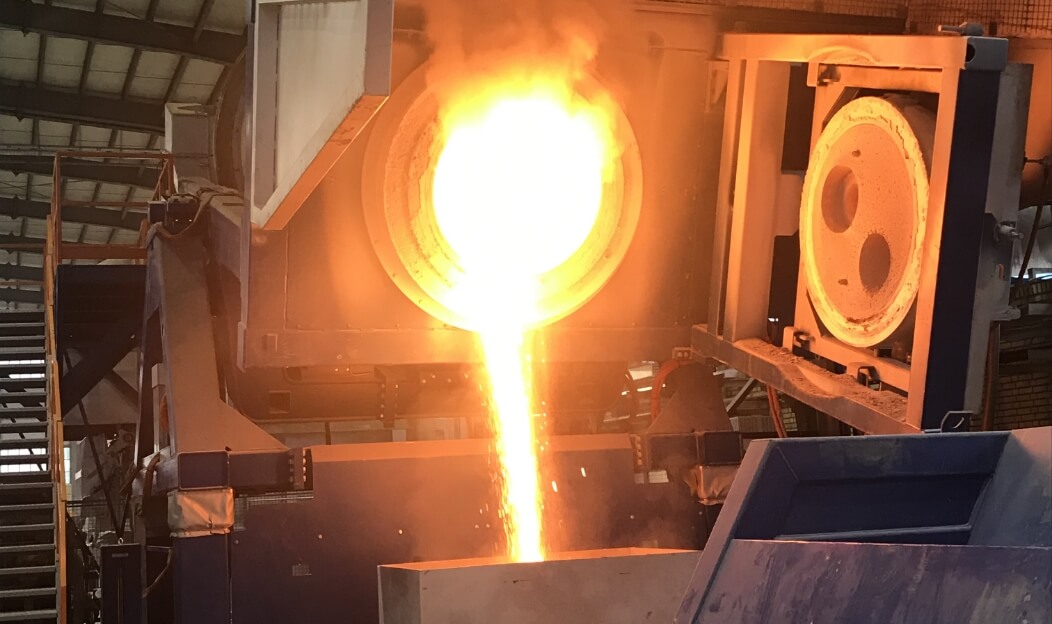
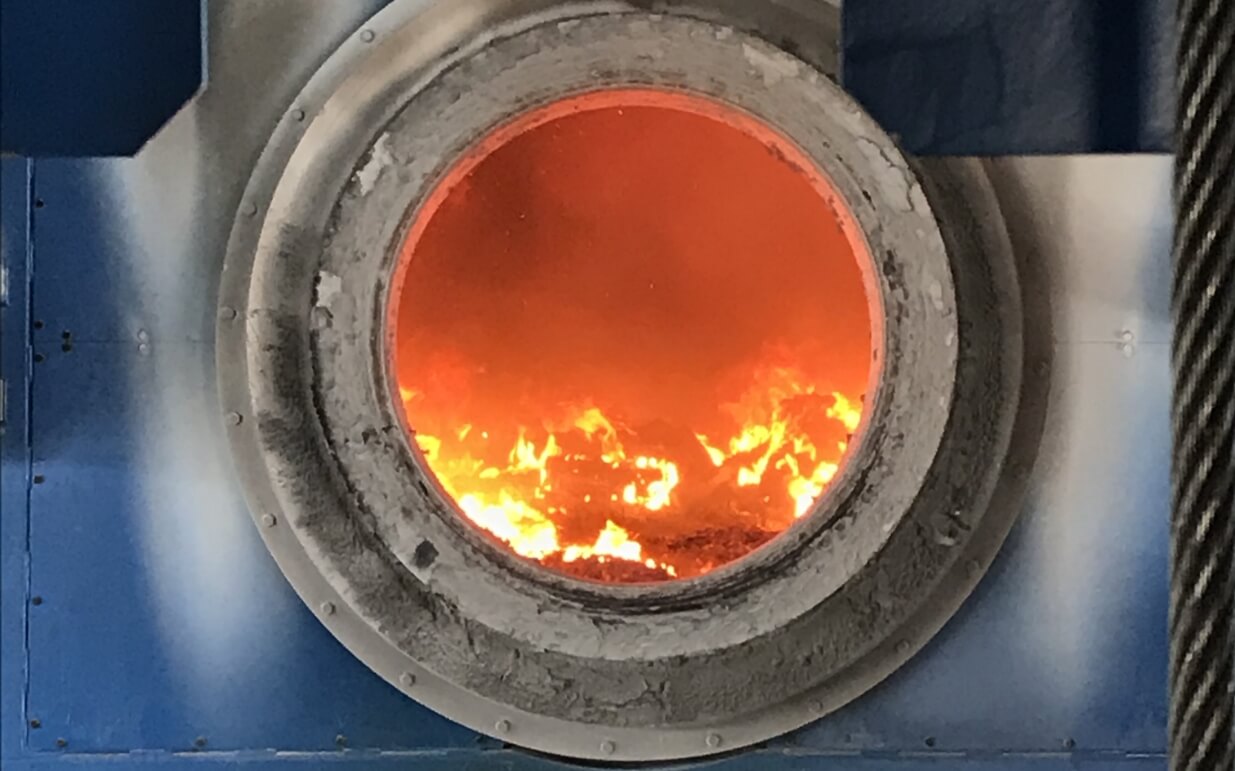
In addition to our portfolio in the aluminium technologies sector, we also offer the COOLmax Dross Cooler. The aluminium-rich dross is cooled to below the required 400 °C within a few minutes and, at the same time, ground to a grain size that enables subsequent separation of the aluminium fraction.
MASTERmax
MASTERmax
Tilting ROTARY
FURNACE

Our exclusive partnership with Gautschi Engineering provides the distribution network for the MASTERmax from KMF, which delivers exciting solutions for sustainable aluminium production. The MASTERmax was specially developed for melting aluminium scrap, including can scrap, dross and chips. We are convinced that the MASTERmax is an excellent choice for our customers´ aluminium production.
The furnaces in the MASTERmax series are characterised by their high performance and energy efficiency. By using molten salt and specifically optimising the melting process, we achieve controlled and effective melting of aluminium scrap plagued by high levels of organic contamination. This enables us to achieve maximum metal yield with minimal energy consumption and significantly reduce CO2 emissions compared to conventional aluminium production. With our method, we are convinced that we can make an important contribution to sustainable aluminium production.
ENERGY EFFICIENT & VERSATILE
The MASTERmax offers another decisive advantage:
its flexibility and adaptability to different melting processes
Thanks to its hybrid design, the furnace can be operated with different melting processes, such as the low-salt and salt-free process, depending on the requirements of the material being recycled. We are convinced that the MASTERmax is the perfect choice for your melting requirements.
This versatility ensures optimal use of the furnace for a wide range of aluminium scrap types and applications. In addition, the flexibility of the furnace ensures efficient and cost-effective production.
Our MASTERmax series furnaces offer you a wide range of sizes. Starting with the compact 1TR2 entry-level model with a 2 MW burner and a capacity of 4 tons, up to the powerful 5TR25 model with a 5 MW burner and an impressive capacity of 50 tons of liquid aluminium.
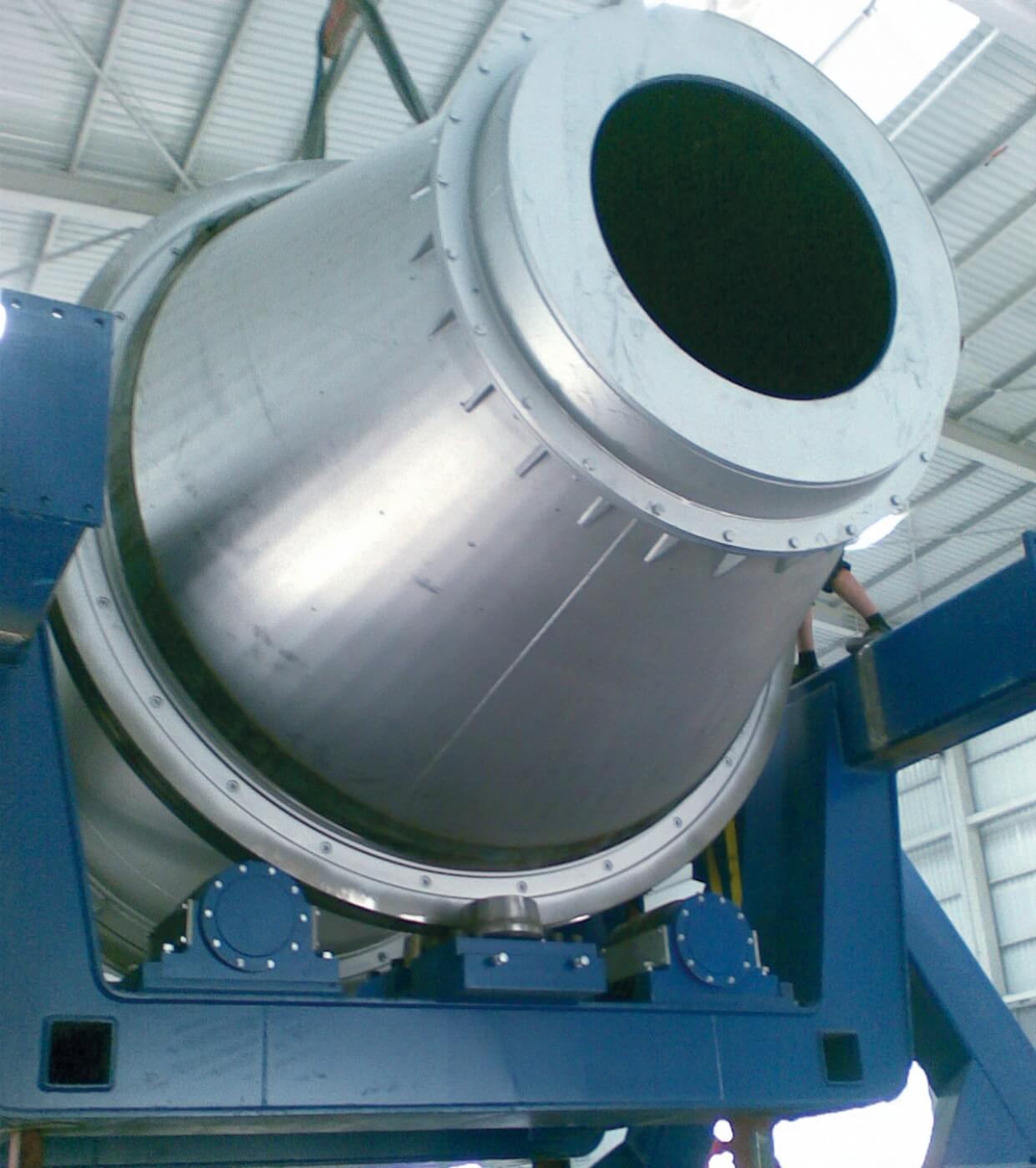
BASE MODEL |
HIGH-END MODEL |
1TR2 2 MW burner 4 t capacity |
5TR25 5 MW burner 50 t capacity |
OTHER FEATURES
The MASTERmax also has a variety of intelligent automation functions that ensure precise and reliable control of the melting process. A variety of practical innovations enable simple and efficient handling of the furnace and minimise energy losses and pollutant emissions. This includes a double-pass exhaust system, a continuously adjustable burner flame length and a fully automatic, 360° rotating loading trough.
The MASTERmax offers a comprehensive solution for aluminium recycling. Overall, the MASTERmax stands out thanks to its high efficiency, flexibility and environmental compatibility. We are convinced that the MASTERmax is an excellent choice for your company. By using the latest technologies, we are helping to make aluminium production more sustainable with the MASTERmax and making an important contribution to the circular economy and environmental protection.
Exclusive distribution of the MASTERmax furnace series by GAUTSCHI.
COOLmax
COOLmax SLAG COOLING
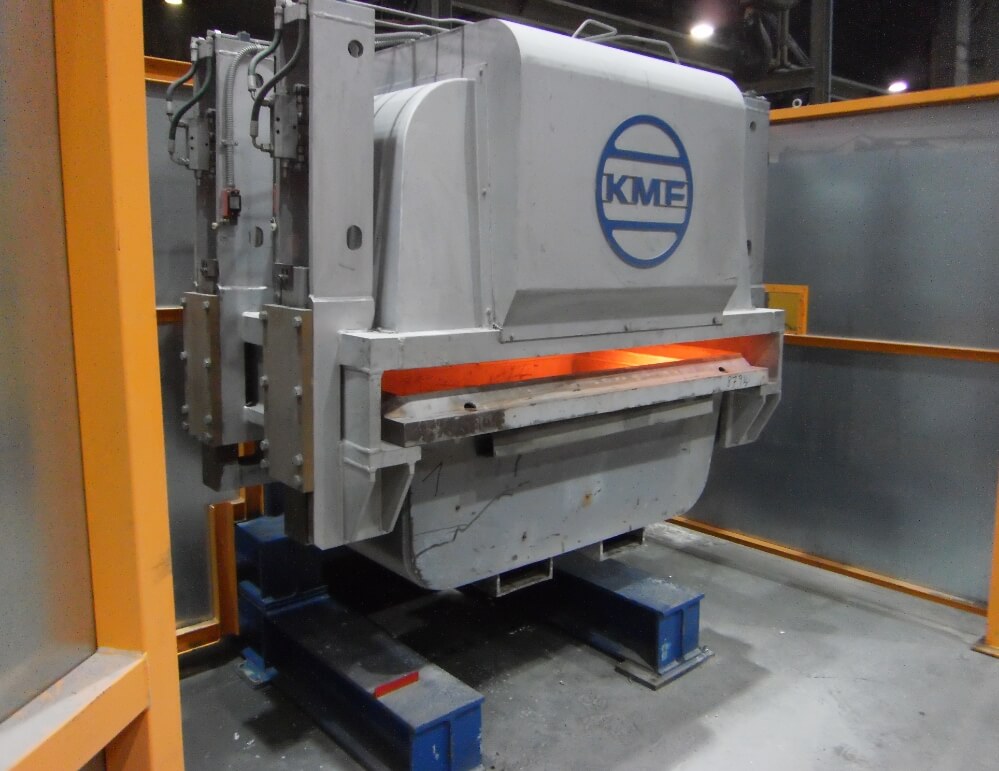
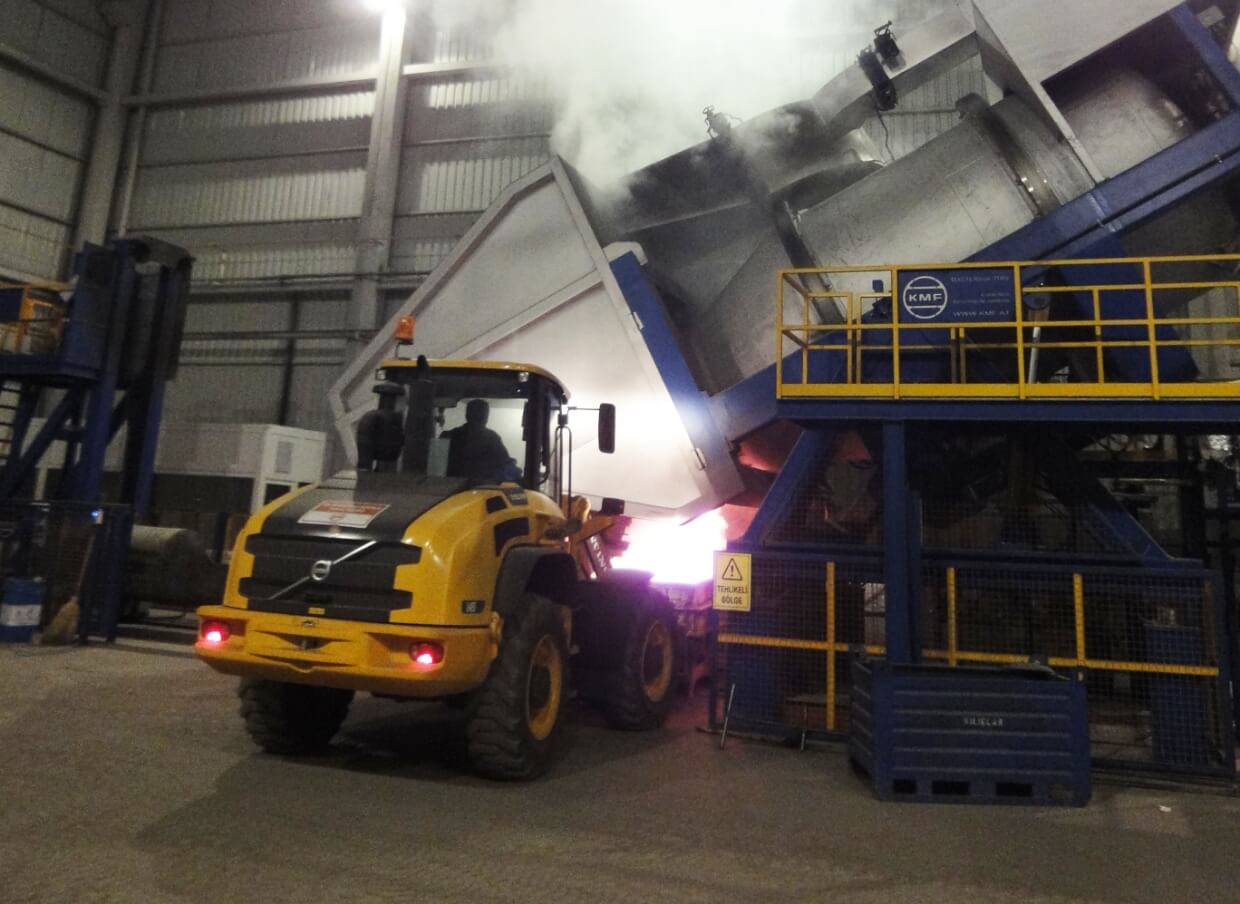
RESOURCE-FRIENDLY & SUSTAINABLE
Slag and dross are by-products of the melting process and contain not only aluminium oxide but also metallic aluminium. To recover this, the slag must be cooled quickly to stop further oxidation.
The COOLmax Dross Cooler from KMF enables rapid cooling below the temperature threshold of 400 °C, at which point self-ignition no longer occurs. This means that more metallic aluminium remains in the residual fraction, which can later be recycled using eddy current separators. Every year, around 4 million tonnes of dross are generated in aluminium foundries worldwide, of which around 1.7 million tonnes of aluminium could be recovered by using the COOLmax Cooler from KMF. Thanks to our innovative technology, we support the aluminium industry in conserving valuable resources and increasing the sustainability of production.
With our reliable and effective cooler unit, our customers can be sure that they are getting the most out of their melting process.